
Boundary layer ingesting (BLI) ducted fan test rig inside the aeroacoustics wind tunnel facility at the University of Bristol. Credit: Feroz Ahmed
Researchers at the University of Bristol have unraveled the mystery behind the noise produced by futuristic aircraft with embedded engines designed to conserve energy.
The study, published in the Journal of Fluid Mechanics, reveals for the first time how noise is generated and propagated from these engines, technically known as boundary layer ingesting (BLI) ducted fans. BLI ducted fans are similar to the large engines found in modern airplanes but are partially embedded into the plane’s main body instead of under the wings. As they ingest air from both the front and from the surface of the airframe, they don’t have to work as hard to move the plane, so it burns less fuel.
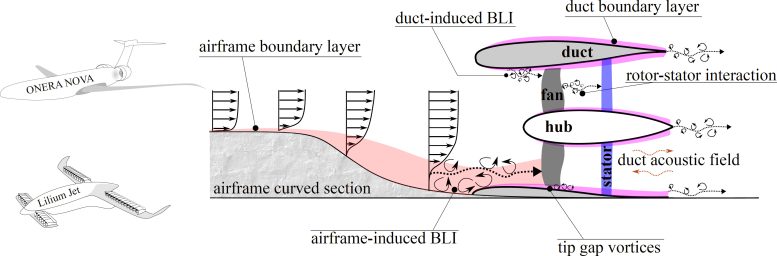
Complex noise sources illustration in an embedded engine or boundary layer ingesting (BLI) ducted fan. Credit: Feroz Ahmed
The research, led by Feroz Ahmed from Bristol’s School of Civil, Aerospace and Design Engineering under the supervision of Professor Mahdi Azarpeyvand, utilized the University National Aeroacoustic Wind Tunnel Facility. They were able to identify distinct noise sources originating from the duct, the rotating fan, and the air flowing over the curved airframe surface.
They found that the noise pattern changes depending on how much thrust the fan is producing. When the fan is producing high thrust, they observed a noise pattern similar to what is seen in fans without ducts. But when the fan is producing less thrust, the noise pattern changes because the duct itself starts making more noise.
Noise in Aviation
Dr Ahmed said: “Our study addresses this urgent issue of noise, which poses a major obstacle in obtaining certifications, by uncovering the physics behind the noise these configurations produce. By understanding the noise mechanisms in BLI ducted fans, it is hoped that industrial guidelines can be developed for quieter airframe-integrated propulsion systems in future aircraft concepts, from large-scale conventional aircraft to small-scale electric vertical take-off and landing, known as eVTOL, aircraft.”
Projects such as the Bell X-22A, Embraer X, Airbus E-fan, Lilium Jet, Green Jet, and Hybrid Air Vehicle are leading the way in developing these systems for next-generation aircraft. They are becoming more popular due to advancements in powerful electric motors.
Dr. Ahmed said: “But, there is a catch for embedded ducted fans — how loud or quiet they are is still a mystery, especially when they are ingesting airflow from around the curved airframe surface.
“Previous research on BLI configurations mostly focused on fans without ducts, where the boundary layer forms over flat airframe surfaces. However, there is a knowledge gap when it comes to the ducted fans ingesting air around curved airframe surfaces, as seen in projects like ONERA NOVA, NASA/MIT Aurora D8, and Airbus Nautilus.
“So, in this study, we have closely examined the various factors that contribute to the noise produced by the embedded ducted fans installed on curved airframe surfaces.”
The researchers designed a BLI test rig featuring an electric ducted fan mounted next to a curved wall, replicating the setup of embedded engines seen in designs like the ONERA NOVA aircraft concept. They collected different types of data from the rig, including measurements of the fan’s thrust output and the amount of noise generated. By dissecting the complexities of noise interaction mechanisms among various sources, this framework helped uncover the underlying physics of where the noise originated and how it changed as the fan operated at different thrust levels.
Conclusion and Potential Impact
Dr. Ahmed concluded: “With the growing demand for a pleasant flight experience with minimum environmental impact, there is a need for quieter aircraft. This research has potential applications in developing strategies to reduce noise emissions in the aviation sector.
“Furthermore, our comprehensive investigation into unlocking the noise contributions in BLI ducted fans has the potential to steer significant research activity within the fluid mechanics community. This, in turn, could foster a deeper understanding and further exploration of aeroacoustics phenomena in ducted fans exposed to a broad spectrum of incoming turbulent flows.
“Our study sheds light on how noise is generated by futuristic embedded ducted fans mounted on curved airframe surfaces, revealing that noise patterns vary with fan thrust levels, offering crucial insights for quieter next-generation aircraft design.”
Reference: “Aeroacoustics of a ducted fan ingesting an adverse pressure gradient boundary layer” by Feroz Ahmed, Ismaeel Zaman, Djamel Rezgui and Mahdi Azarpeyvand, 15 April 2024, Journal of Fluid Mechanics.
DOI: 10.1017/jfm.2024.134
This research, sponsored by the European Union’s Horizon 2020 research and innovation program under the ENODISE (Enabling optimized disruptive airframe-propulsion integration concepts) project grant agreement number 860103, was conducted in collaboration with ONERA – the French Aerospace Lab, and several other partners.